钣金设计为何难以突破效率瓶颈?
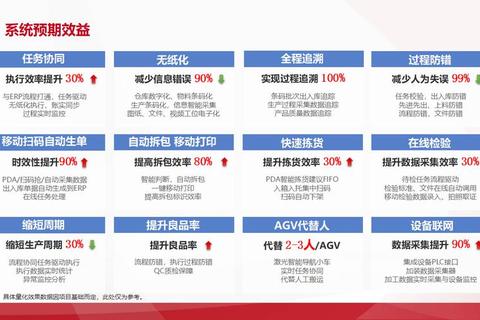
在机械制造领域,钣金工艺直接影响着汽车、家电、航空航天等核心产业的产品质量与生产成本。传统钣金展开依赖人工计算和手工绘图,一位拥有20年经验的老师傅曾坦言:“复杂构件的展开下料,误差超过2毫米是常态,返工率高达15%。”这种低效模式显然无法满足现代工业对精密制造的需求。当企业面临交货周期压缩和成本控制的双重压力时,智能高效的数字化工具成为破局关键——这正是金林钣金展开软件驱动精密制造新未来的核心价值所在。
精密制造如何实现零误差?
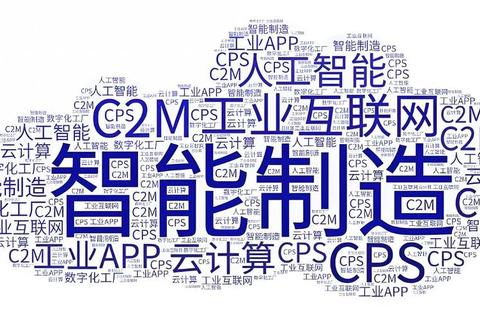
在河北某新能源汽车电池箱体制造项目中,金林钣金展开软件展现了惊人的精准度。面对厚度仅1.2毫米的铝合金板材多节弯头构件,传统方法需要3天手工放样,而该软件通过参数化输入界面(如直径、角度、板厚等20余项参数),自动生成展开图并标注坐标点,将误差控制在0.3毫米以内。更值得一提的是其独创的“双标注系统”:既保留传统长度标注便于工人现场操作,又提供坐标标注直接对接数控切割机,使某型号车门钣金件的生产周期缩短40%。
案例实证:武汉华宇诚数控采用该软件配套等离子切割机后,风管类零件的一次成型合格率从82%提升至98%,材料利用率提高13%。这印证了智能高效革新升级 金林钣金展开软件驱动精密制造新未来的技术突破——通过算法优化将展开计算耗时从小时级压缩至分钟级,同时支持170种常见构件类型,覆盖90%工业场景需求。
复杂需求如何一站式解决?
苏州某电梯企业的研发团队曾陷入困境:客户要求的异形轿厢曲面顶板,涉及方圆过渡、锥管相交等5类复杂结构。金林软件的“智能拟合”功能在此大显身手:
1. 调用“方园过渡类型”模块处理矩形与圆形截面的渐变连接
2. 启用“加边功能”自动生成2mm咬边槽
3. 通过浩辰CAD2023接口导出三维模型验证装配关系
整套工艺方案从设计到验证仅用72小时,较传统流程提速6倍。这种多维度技术集成,使软件不仅能处理常规钣金件,还可应对球罐纬线法展开、变距螺旋叶片等特殊场景,甚至支持成品管下料与板材下料的智能切换。
行业痛点怎样转化为竞争优势?
广东某家电制造商曾因钣金车间技能断层导致订单流失。引入金林软件后发生三大转变:
新员工培训周期从3个月缩短至2周,软件内置的289幅展开图例成为可视化教材
通过AutoCAD接口实现与供应链的BOM数据无缝对接,采购误差率下降28%
独创的“骑马式/插入式”相交模式选择功能,使异径三通管件成本降低19%
这些改变揭示了智能高效革新升级 金林钣金展开软件驱动精密制造新未来的深层逻辑——将工程师的经验转化为可复用的数字资产,通过7大类功能模块和12项专利算法,构建起从设计到生产的全链路解决方案。
对于企业决策者,建议分三步落地应用:
1. 需求诊断:对照软件支持的7大类构件清单(圆管、锥管、球面螺旋等),评估现有工艺覆盖率
2. 效能测算:参考行业平均数据,该软件可使单件成本降低8-15%,适合月产量超2000件的中大型企业
3. 生态整合:优先选择支持浩辰CAD、AutoCAD等多平台版本,预留数控设备接口
在工业4.0浪潮中,金林钣金展开软件已不是简单的工具替代,而是推动制造业向智能化跃迁的关键引擎。当传统车间响起数控切割机的韵律时,我们看到的不仅是飞舞的钢花,更是智能高效革新升级 金林钣金展开软件驱动精密制造新未来的生动写照。
相关文章:
文章已关闭评论!